Beyond regulations, towards sustainable mobility with Heesung Catalysts
Heesung Catalysts provides green mobility solutions for a sustainable future. Recognising the environmental problems caused by the use of fossil fuels, we have developed innovative catalyst technologies that effectively reduce harmful emissions from automobiles. In the automotive sector, we supply high-performance 'catalysts for automotive exhaust purification' that purify carbon monoxide (CO), nitrogen oxides (NOx), and particulate matter (PM) to meet strict emission regulations in each country and contribute to improving air quality.
Gasoline Catalysts
Petrol engines using gasoline are a key source of power for passenger vehicles, providing high revs and smooth driving. However, the combustion process involves the mixing and ignition of fuel and air, which is prone to incomplete combustion, resulting in harmful emissions such as hydrocarbons (HC), carbon monoxide (CO), and nitrogen oxides (NOx). As global air pollution concerns have increased, major countries such as Europe, the United States, and South Korea have introduced increasingly stringent regulations to reduce emissions from vehicles. These regulations require technical solutions to reduce the allowable levels of NOx, HC, and CO emitted from petrol vehicles and to control them effectively.
Heesung Catalysts' gasoline exhaust purification catalysts are an essential technology to address this issue. Centered around Three-Way Catalysts (TWC), they convert harmful emissions from petrol engines into air-friendly substances to meet regulatory standards while maintaining engine performance and fuel economy. Additionally, Gasoline Particulate Filters (GPF), which reduce fine particles (PM), and Lean NOx Trap (LNT) technology, which efficiently stores and purifies NOx, play a critical role in meeting tightened environmental standards.
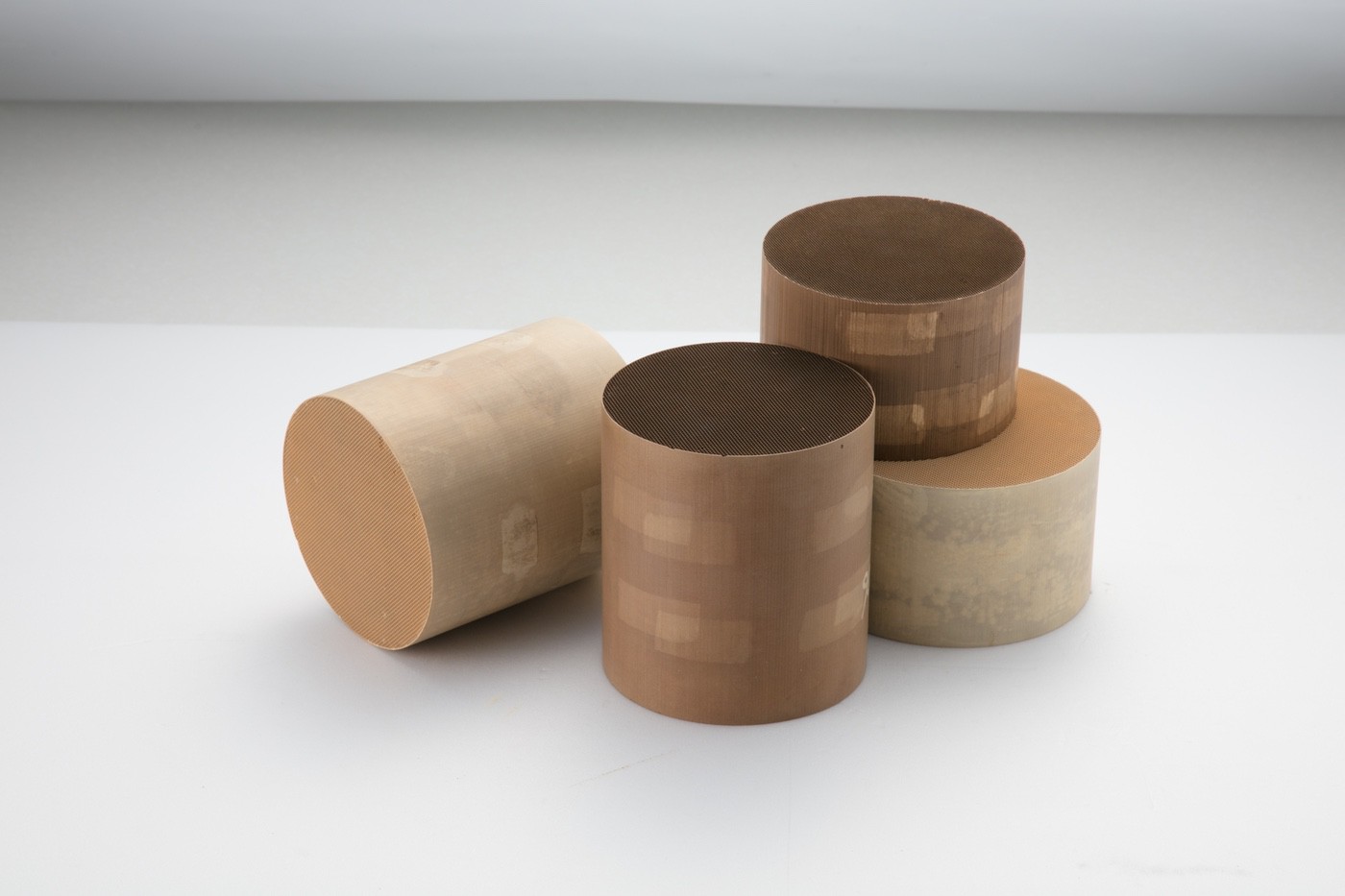
Three-Way Catalysts (TWC)
Three-Way Catalysts (TWC) are the oldest catalysts for automotive emission control, first developed in the U.S. in the mid-1970s. Initially, as two-way catalysts, they were designed to remove hydrocarbons (HC) and carbon monoxide (CO). In the early 1980s, the introduction of ceria (CeO₂), a material capable of storing and releasing oxygen depending on exhaust gas composition, led to the creation of the first Three-Way Catalyst (TWC). This innovation allowed TWC to reduce three major pollutants simultaneously: hydrocarbons (HC), carbon monoxide (CO), and nitrogen oxides (NOₓ) emitted from gasoline vehicles. Since then, ongoing research and development have focused on improving performance to meet stricter emission standards, advancing new engine technologies, and addressing fluctuations in precious metal prices, leading to the development of various types of TWC products.
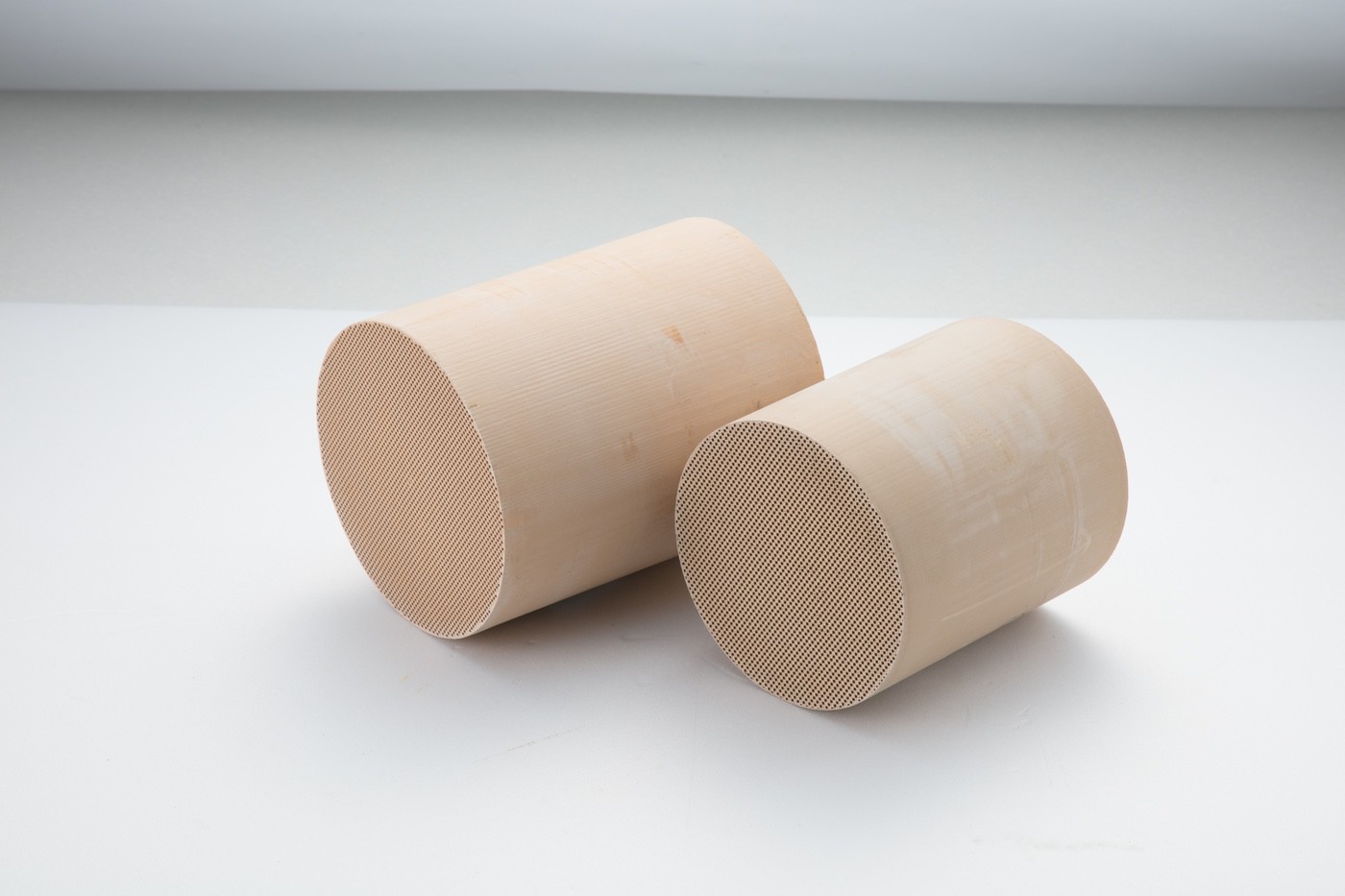
Gasoline Particulate Filter (GPF)
To meet stricter emissions and CO₂ regulations, improve fuel efficiency, and increase power, gasoline vehicles are transitioning from multi-point injection (MPI) to direct injection (GDI) systems. While GDI engines offer many advantages, they produce a significant number of nano-sized particulate matter (PM) particles due to uneven combustion during cold starts and high-load operation. The Gasoline Particulate Filter (GPF) integrates Three-Way Catalyst (TWC) technology with porous ceramic filters (Wall-Flow) to address PM emission regulations. It is primarily used in vehicles sold in Europe and China that feature direct injection engines.
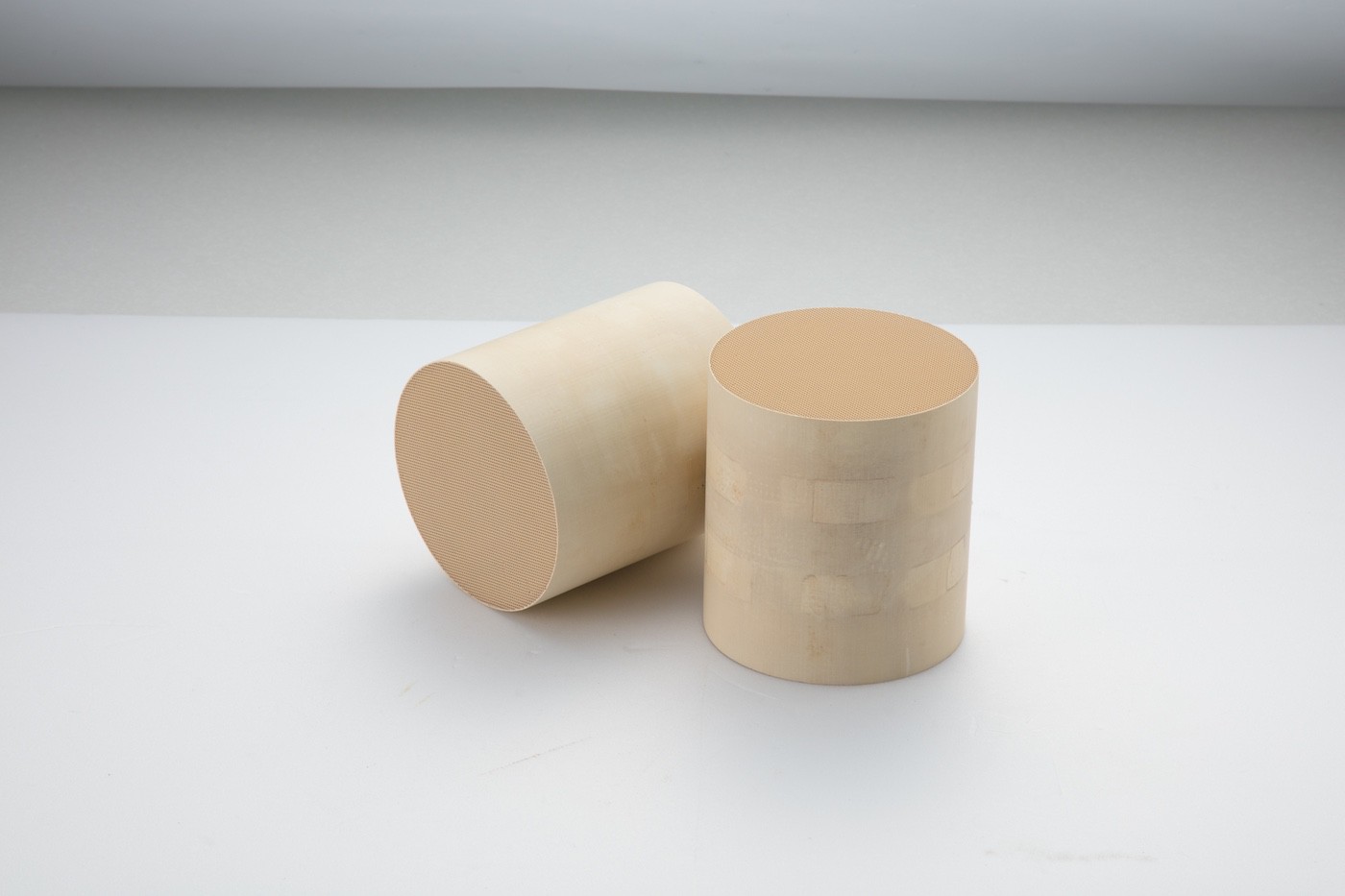
NOx Trap
A typical petrol car is designed to operate the engine around the theoretical power ratio condition (λ=1) to maximise the purification efficiency of the ternary catalyst.To reduce greenhouse gases such as CO₂ and improve fuel efficiency, research has increased on engine controls that extend lean-burn conditions, where fuel is scarce and air is abundant. Under these conditions, NOx emissions, which occur during combustion, are chemically difficult to reduce. To improve this, we have developed the world’s first gasoline NOx Trap catalyst, which can contribute to NOx purification and improve vehicle fuel efficiency. Gasoline NOx Trap technology is classified as follows according to catalyst characteristics and requires optimised development in consideration of catalyst characteristics, driving conditions and environment during vehicle development.
PremAir
Ozone (O3), which is produced in the atmosphere by nitrogen oxides (NOx) and volatile organic compounds (VOCs) emitted from car exhausts, mainly in the summer, in the presence of ultraviolet radiation, causes damage to human health (eyes, respiratory system) and reduced crop yields. PremAir is a catalytic device that coats a catalytic material onto the surface of the radiator, the coolant heat exchanger in a car, to break down ozone (O3) into oxygen (O2) during vehicle operation. The U.S. Environmental Protection Agency (EPA) provides some relief from the level of emissions regulations to which vehicles equipped with PremAir catalysts must respond. This catalyst is expected to become increasingly useful in the future as emissions regulations continue to tighten.
Evap Trap
Evap Trap is a catalytic technology that removes volatile organic compounds (VOCs) — the fuels that vaporize from the engine’s intake port and fuel tank and are discharged into the atmosphere when a gasoline vehicle is stopped or the engine is off. These compounds are absorbed by catalytic materials coated on the surface of the air cleaner box and canister, and then circulated into the engine’s combustion chamber for combustion when the vehicle is restarted. This technology is expected to gain increased attention in the future as related regulations are being strengthened not only in Korea but also in major countries such as North America and China.
Diesel Catalysts
Diesel engines offer high fuel efficiency and powerful torque, and are widely used in commercial and heavy-duty vehicles. However, the combustion of diesel fuel produces harmful emissions such as nitrogen oxides (NOx), particulate matter (PM), carbon monoxide (CO), and hydrocarbons (HC). In particular, the high temperature/high pressure combustion characteristics of diesel engines increase the generation of NOx and particulate matter, which are major contributors to air pollution and health problems. As a result, emission regulations for diesel engine vehicles have been tightened globally, and a technological response to address this is essential. Heesung Catalysts offers solutions with state-of-the-art technologies such as selective catalytic reduction (SCR), diesel oxidation catalysts (DOC), diesel particulate filters (DPF), and NOx traps (LNT) to efficiently purify emissions from diesel engines.
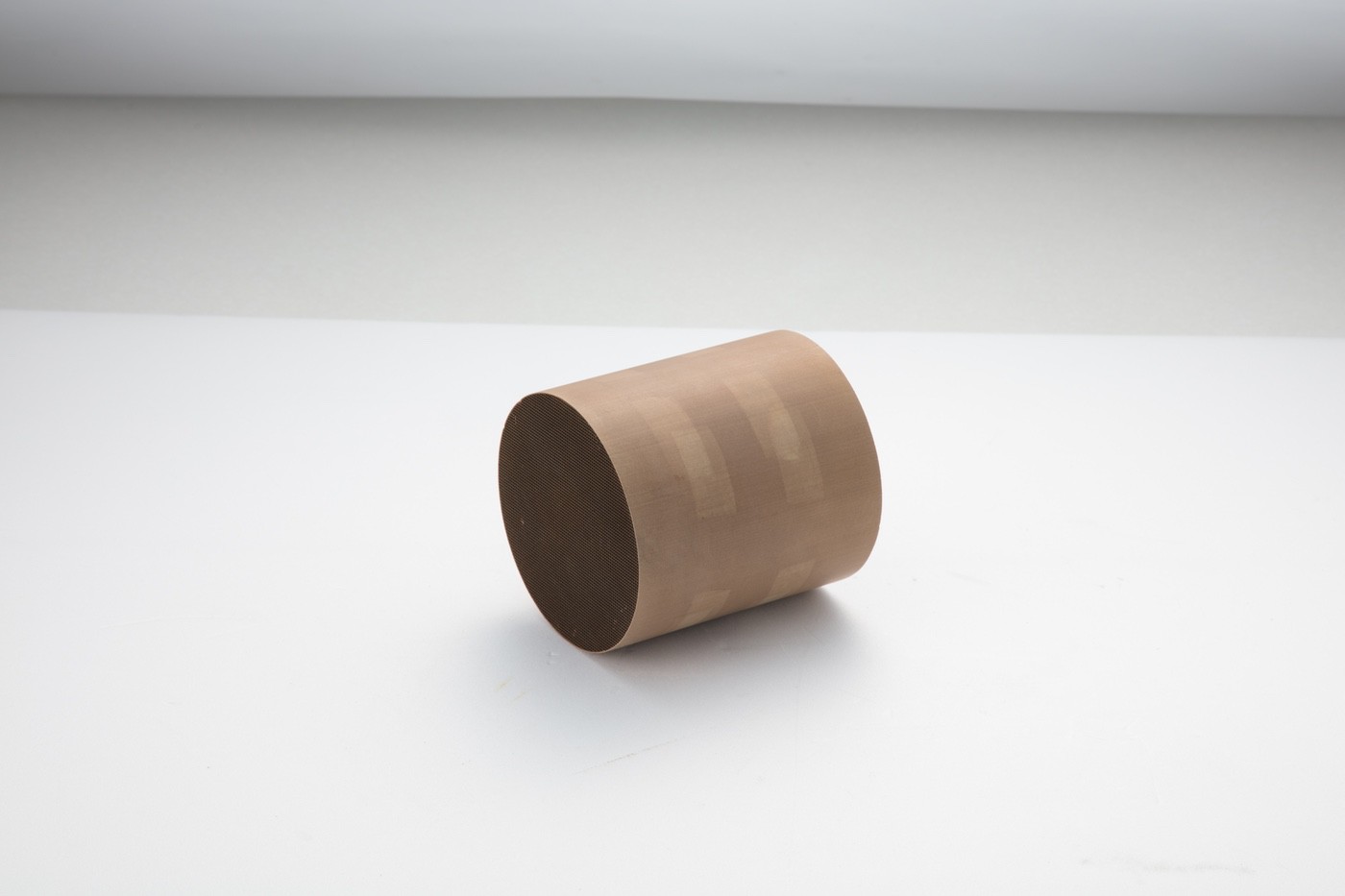
Diesel Oxidation Catalysts
Diesel oxidation catalysts (DOC) are the oldest of the various diesel catalyst technologies and are still the most commonly used catalysts in diesel vehicles (including non-road vehicles). The main role of DOC is to oxidise and remove gaseous hydrocarbons (HC) and carbon monoxide (CO), and to oxidise and remove the soluble organic fraction (SOF) of particulate matter (PM). It can also perform additional functions to improve the performance of other catalysts (diesel particulate filters, selective catalytic reduction catalysts, etc.) located downstream of the DOC in catalytic systems for various diesel engines.
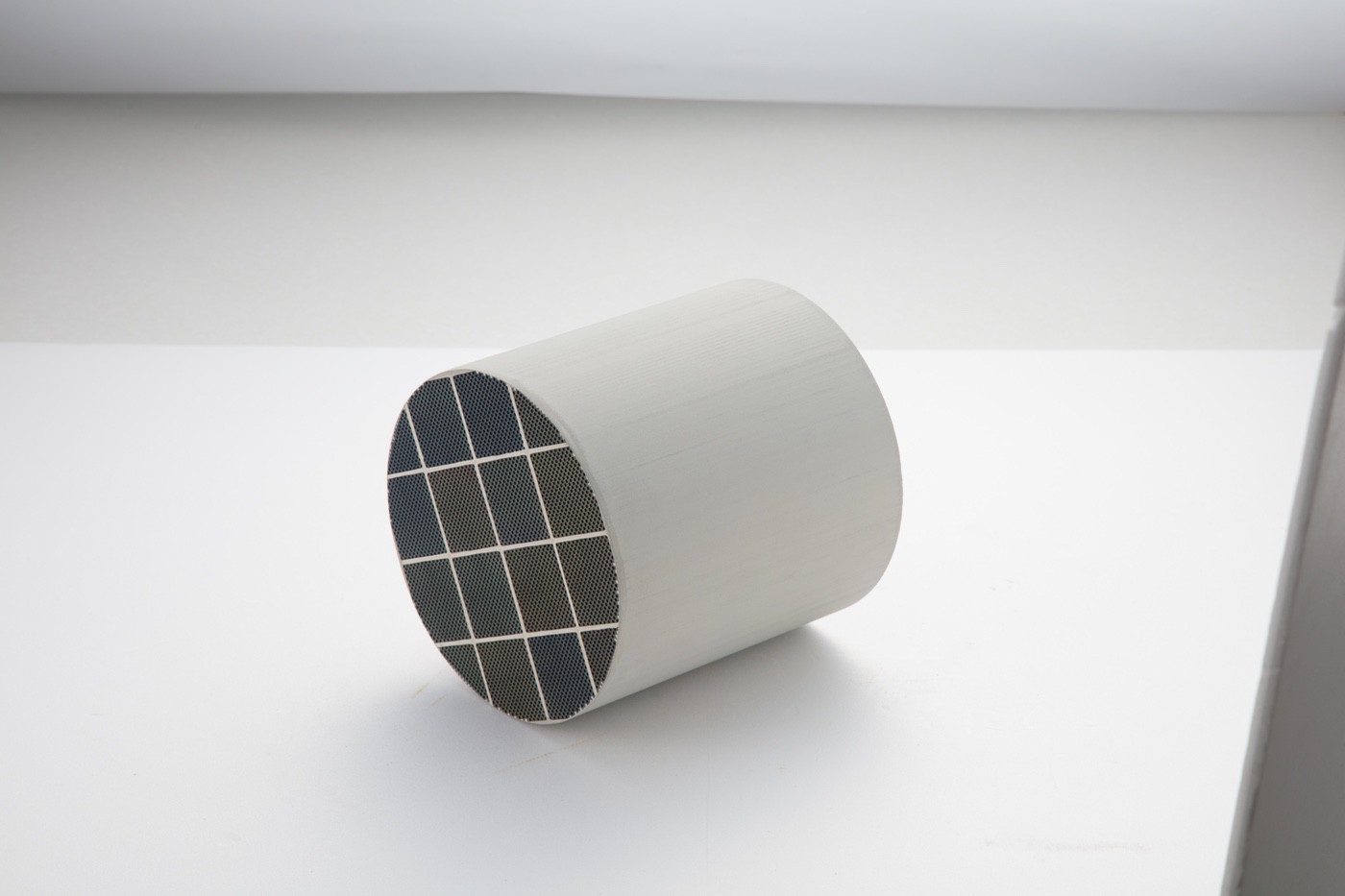
Diesel particulate filters
Diesel particulate filters (DPFs) are also known as catalysed soot filters (CSFs). It was developed by BASF (formerly Engelhard), a joint venture company, for the first time in the world, and has been used since the PM (Particulate Matters) regulations began in earnest, and is installed in most diesel vehicles. In addition, DPFs with multiple functions (hydrogen sulphide removal, nitrogen oxide removal, etc.) have been developed and supplied to minimise the size of the catalytic system to respond to the stricter diesel vehicle emission regulations. Diesel particulate filters (DPFs) require periodic high-temperature removal of particulate matter (PM) trapped inside (DPF regeneration), which increases the internal temperature by up to 1000 degrees or more, so thermal durability must be ensured. Various filter materials are used for this purpose, and the filter material/properties and catalyst properties (composition, manufacturing process, etc.) must be optimised to supply DPFs with excellent performance.
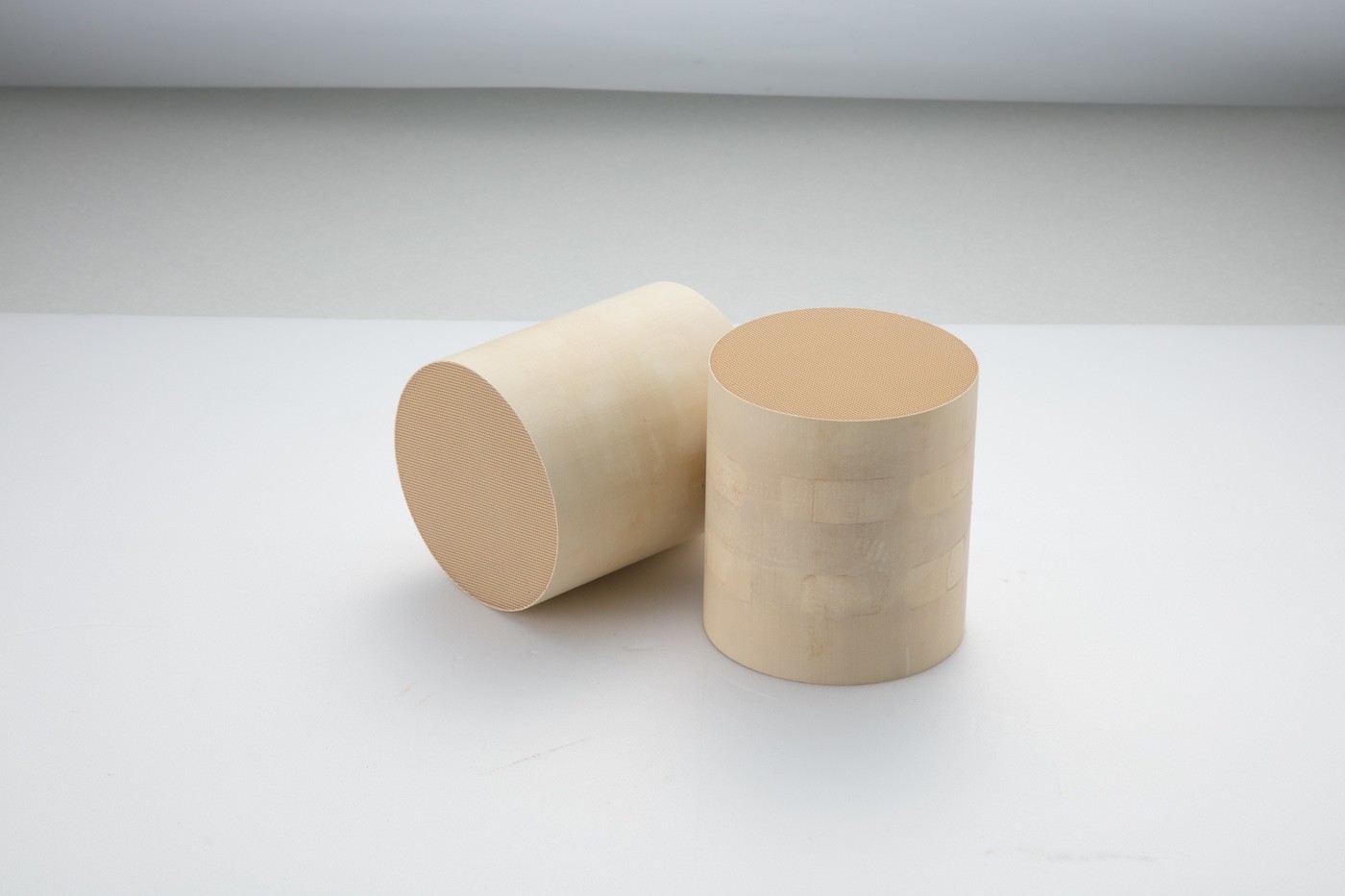
Diesel Lean NOx Trap (LNT)
Purifying nitrogen oxides (NOx) emissions in lean-burn diesel engines (oxygen-rich combustion) is particularly challenging. The Diesel Lean NOx Trap (LNT) incorporates NOx-adsorbing components that chemically trap NOx during lean-burn operation. To sustain NOx purification performance, the LNT catalyst requires periodic regeneration. This is achieved by temporarily switching the engine to a fuel-rich condition (oxygen-deficient) to release the stored NOx and convert it into harmless nitrogen (N₂). Due to the complexity of the chemical reaction mechanisms involved, significant effort is required during vehicle development to optimize LNT operation.
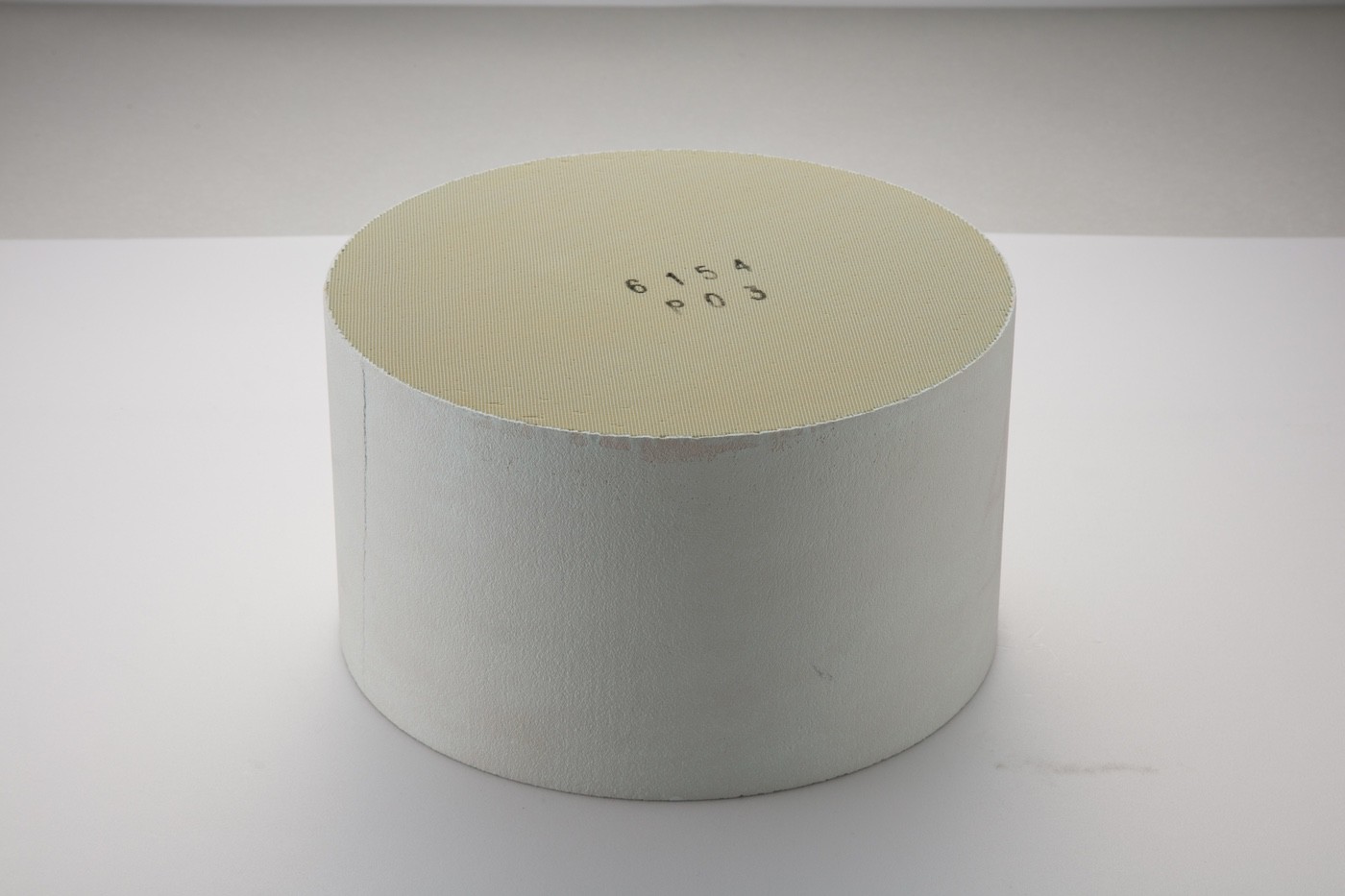
Selective Catalytic Reduction (SCR)
Two main technologies purify NOx emissions from diesel engines: Lean NOx Traps (LNT) and Selective Catalytic Reduction (SCR). SCR injects a colorless, odorless urea solution into the exhaust gas to generate ammonia (NH₃), which reacts with NOx to convert it into harmless nitrogen (N₂). Heesung Catalysts is a leader in SCR technology for stationary and automotive applications, leveraging expertise to meet NOx emissions regulations. In addition to traditional vanadium-based technologies, Heesung offers advanced zeolite-based SCR catalysts with exceptional thermal durability and low-temperature performance.
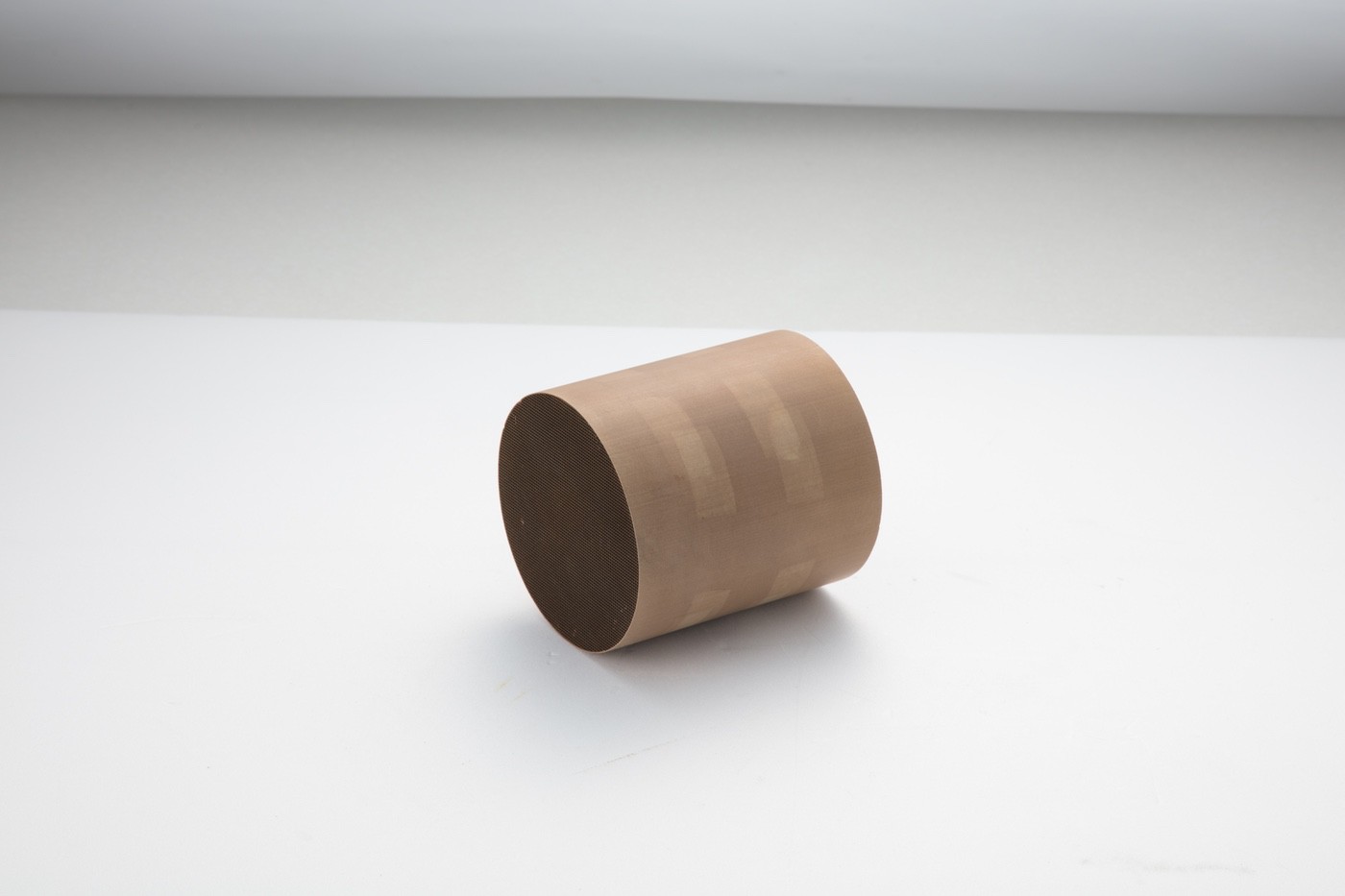
Ammonia Oxidation Catalyst (AOC)
Ammonia purification catalysts (AOC) are catalysts that are placed downstream of selective catalytic reduction (SCR) catalysts to convert ammonia (NH3) that is unreacted and emitted from the SCR catalyst into harmless nitrogen (N2) rather than nitrogen oxides (NOx), Our unique patented catalyst technology can purify ammonia (NH3) to nitrogen (N2) under ammonia (NH3) and oxygen (O2) conditions and nitrogen oxides (NOx) under ammonia (NH3) and nitrogen oxides (NOx) conditions through selective catalytic reduction (SCR). To meet increasingly stringent emissions regulations, we offer high-performance ammonia oxidation catalysts (AOC) in various combinations with selective catalytic reduction (SCR) catalysts to meet customer requirements.